TRANSFORMER
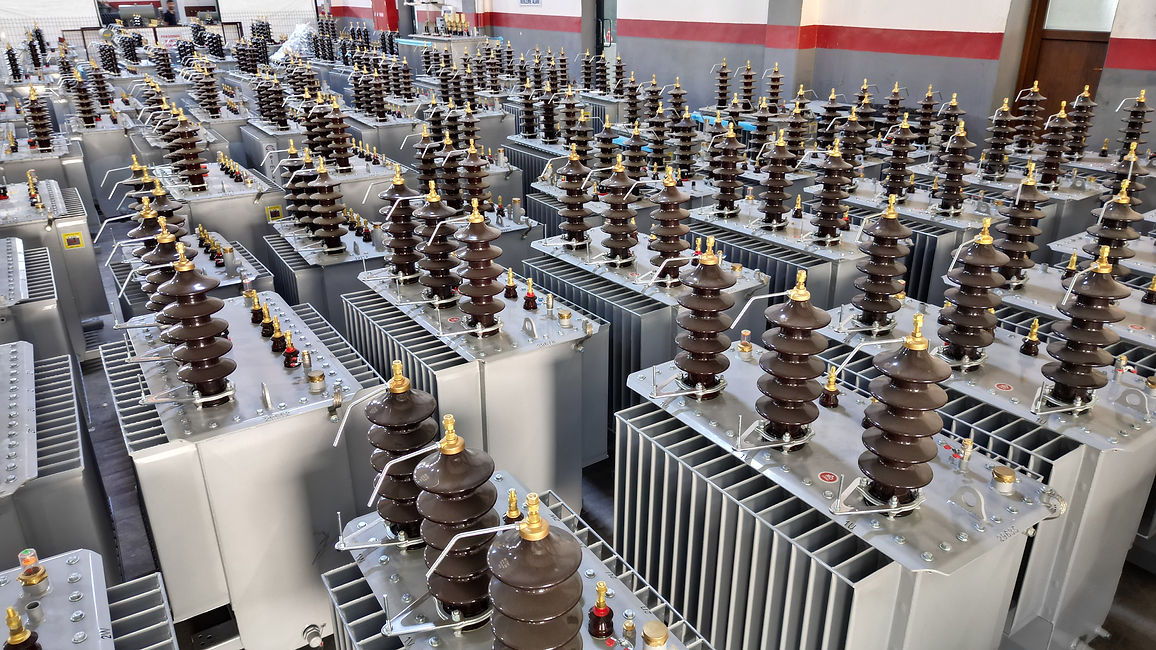
Our Transformers

Dressing
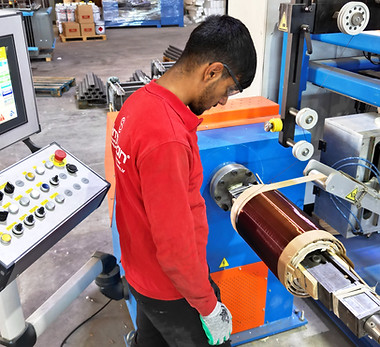
DRESSING
Distribution Transformers Windings: Low voltage winding conductor is copper. Layer insulation in sheet windings is provided with thermally improved resin paper (DPP).
Active Part

ACTIVE PART
In order to form the active part of the transformer with ready core and coils, the coils are mounted by being compressed against the core and each other by means of slats in order to carry radial forces and the upper yoke is arranged. At the same time, the coils are equipped with a protection system against axial forces. The necessary welding and connections of the adjustment ends going to the commutator or step switch are made with silver electrodes and the active part is made ready for the furnace.
Boiler
.png)
BOILER
It is used for the protection of cooling and insulation material in oil type transformers. Depending on the cooling surfaces, transformers up to 3150 KVA are manufactured with corrugated walls, and transformers with larger powers are manufactured with radiator tanks.
Drying and oil filling
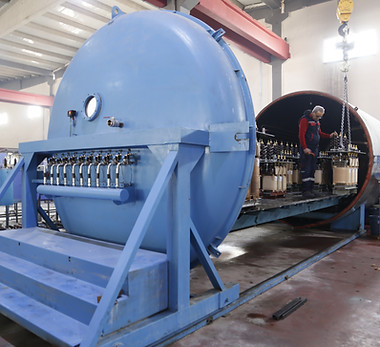
DRYING AND OIL FILLING
Transformers, whose active part assembly is completed, are dried in drying ovens at 120 degrees and then placed in tanks and filled with oil in the vacuum chamber.
In the vacuum chamber, the air remaining in the transformer tank is sucked and the insulation oil is fully penetrated into the active part. The filled oil provides insulation and cooling.
Painting

PAINTING
The boilers that are manufactured are painted by spray method. Standard painting consists of one primer and two layers of final paint. Total film thickness is not less than 105p. Standard transformer color is RAL7033, also known as cement gray.
It is possible to paint in different structures (such as zinc coating), different thicknesses and different color codes according to customer requests.
Magnetic Circuit

MAGNETIC CIRCUIT
It is core type and manufactured from 0.30, 0.25 and 0.23 mm thick M5, M4 and M3 silicon alloy sheets with oriented crystals. 45 degree inclined cut sheets are used in the transition areas of the magnetic circuit. All sheets used in the magnetic circuit are cut by CNC controlled cutting machine, stacked and arranged to form the magnetic circuit. Magnetic circuit cutting and arrangement is done with a method called step-lab which minimizes iron losses. The core is arranged with cross and longitudinal step-lab applications.